Floor coverings and recommended adhesives
Flooring adhesives
Adhesives need to meet special requirements if they are to produce a reliable bond between the floor covering and the properly prepared substrate. When bonding textile floor coverings, for instance, it must be ensured that the adhesive also survives shampooing or cleaning by spray extraction without damage and that the adhesive reliably secures the flooring even when it is wet.
Adhesives for bonding PVC flooring must be resistant to plasticizers, whereas rubber flooring adhesives must feature excellent adhesion to rubber. Naturally, parquet adhesives must be able to withstand the natural shear and shrinkage forces of wood.
Today, modern dispersion adhesives are primarily used. In addition to their many technical features, they also offer special advantages with respect to indoor air quality.
Well over 90 % of Thomsit’s flooring installation products have been awarded the EMICODE, in some cases also the Blue Angel eco label. This means that very low-emission adhesives are now available to cover all applications in flooring technology.

When applying dispersion adhesives, some important factors need to be considered. Besides the type of substrate, this also includes the notch size of the trowel, the flash-off time, the open time and the load-bearing strength.
The notch size determines how much adhesive is applied to the surface.
The most frequently used notch size for resilient flooring is A2, for textile flooring B1. The Technical Data Sheets specify the notch size to be used for the respective product. For more detailed information on notched trowels please refer to TKB Technical Briefing Note 6 "Trowel Notch Sizes", issued by Industrieverband Klebstoffe/German Adhesives Industry Association (www.Klebstoff.com).
The flash-off time is the time between applying the adhesive and placing the floor covering into the adhesive bed. During this time, a large part of the moisture contained in the adhesive usually evaporates and initial tack develops. The flash-off time considerably depends on the ambient conditions and on the substrate. Especially on absorbent substrates, the flash-off time must not be too long as the adhesive ridges may already have hardened before the flooring is placed on top. Even with a pressure roller the hardened adhesive ridges can no longer be flattened.
The consequence: The adhesive ridges will only be flattened when a point load like a chair or table leg is applied. As a result, permanent impressions may show in the floor covering.
Open time means the limited time after application of the adhesive during which the floor covering can be placed into the adhesive bed while still achieving full, uniform wetting of the underside of the flooring. If this time is exceeded, a sufficiently strong bond is no longer possible. The open time of an adhesive very much depends on the ambient conditions.
The load-bearing strength of an adhesive indicates exactly when the bond becomes load-bearing and the bonded surfaces can be put to full use.
After the floor covering has been laid, it is always necessary to press it down with a rubber roller. This will produce a firm bond with the adhesive and flatten the adhesive ridges, which is of great importance for the later appearance of the surface.
A special connection exists between the levelling compound and the adhesive. The smoother the levelled surface, the more uniform the adhesive layer and the lower the amount of adhesive required. Naturally, this also influences the later appearance of the finished floor.
IMPORTANT!
Always observe short flash-off times on absorbent substrates to avoid later impressions. Non-absorbent substrates require long flash-off times until the adhesive has dried. Only use adhesives that have been specially designed for this purpose. Remember that only special types of flooring can be used on non-absorbent substrates.
Please refer to the Technical Data Sheets for more detailed information.
Textile flooring
Textile floor coverings are usually classified according to their manufacturing process: this determines the measures to be taken for their installation. They are equipped with different types of backing. The backing, in turn, determines the proper choice of adhesive.
The following rough classification of backings can be made:
- Foam backing
- Smooth foam backing
- Embossed foam backing
- Waffle-type foam backing
- Textile backing
- Non-woven (or fleece) backing
- Heavy backing
- Precoating (for reinforcing the backing)
Woven carpeting
Woven carpeting is available in two variants: flat carpeting and pile carpeting, depending on the manufacturing process. Basically, woven coverings have a grid-like underside.
High-quality adhesives like Thomsit T 410 or UK 800 are the adhesives of choice for bonding this type of covering: they feature extra high initial tack and a very long open time. Woven carpeting can be very unwieldy and difficult to handle. Due to the pattern repeat, a sufficiently long correction time is required for adjusting the seams.
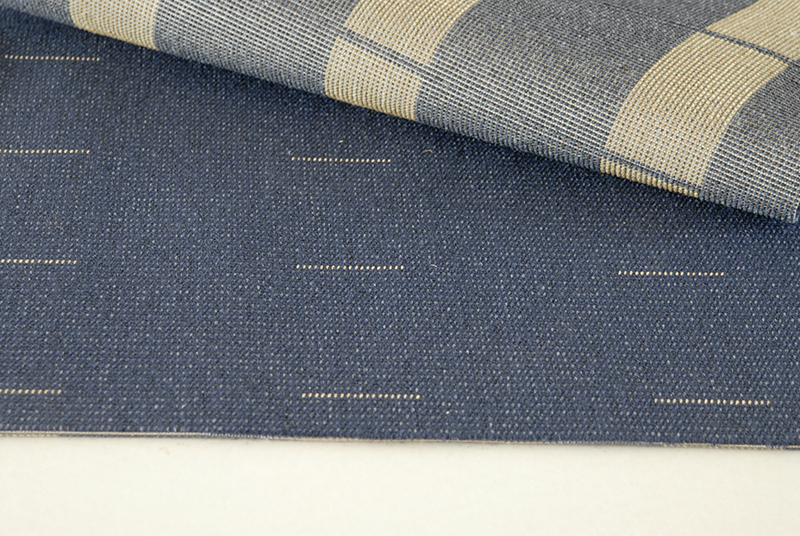
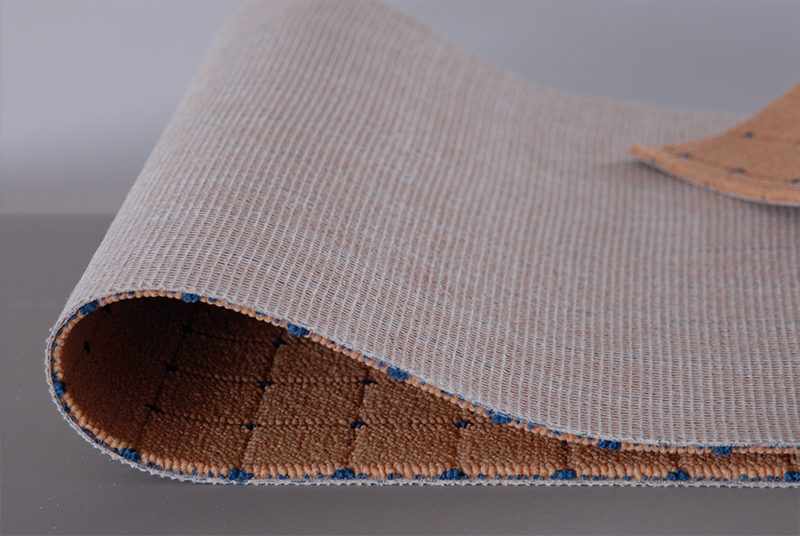
Tufted carpeting
Tufted floor coverings are easily recognizable in cross-section by the loop pile or cut pile surface. Cut piles are formed by cutting open the loops so that small "tufts" are created. Tufted carpets are produced on multiple-needle sewing machines up to 5 meters width.
All Thomsit carpet adhesives are well suited for bonding this very common type of carpeting.
Needle-punch or low-loop pile carpeting
Both the needle-punch and the low-loop pile variants are particularly hard-wearing and therefore often found in heavy-duty environments like open-plan offices. Just like woven carpeting, this type of textile flooring has a reputation for being unwieldy.
This is why carpet adhesives with a very high bonding strength must be used for this type of flooring.
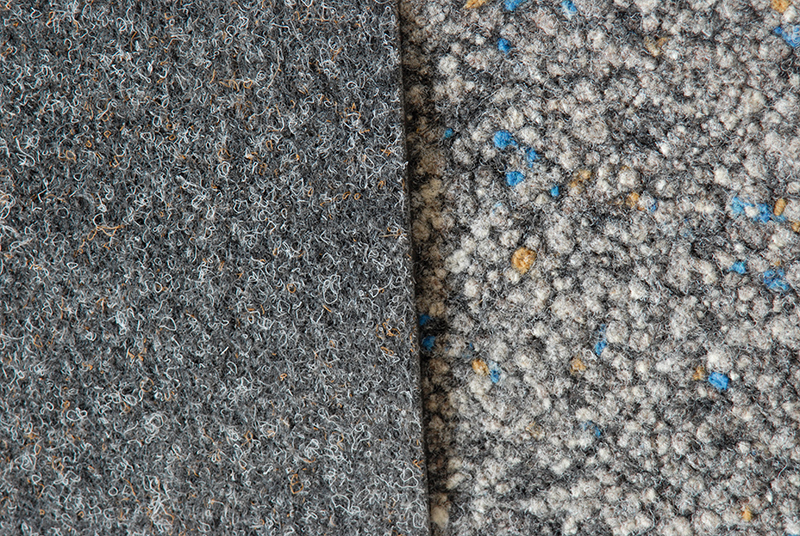
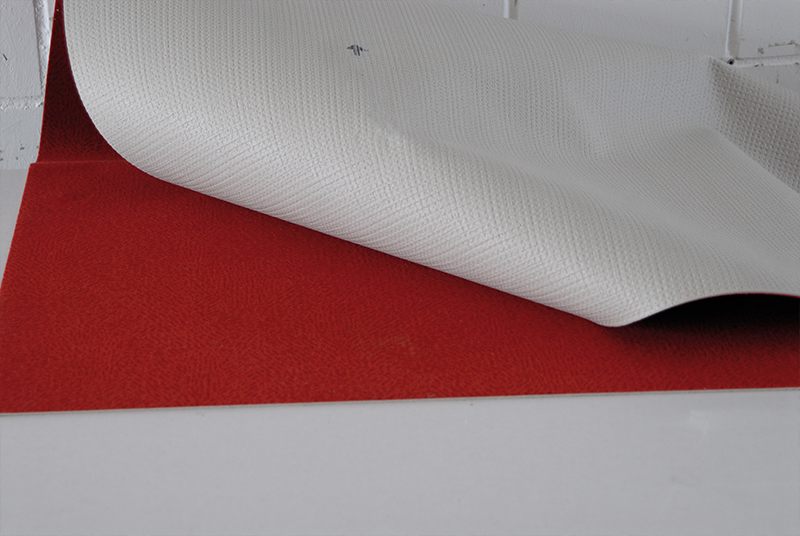
Flocked coverings (flocked textile flooring)
Flocked coverings are produced with a PVC foam backing. Their upper side consists of pile fibers inserted vertically into a carrier layer.
For bonding this plasticized material, we recommend using Thomsit K 188 E (trowel notch size A2 or A3).
Resilient flooring
Resilient flooring primarily includes PVC, CV, rubber and linoleum coverings but also polyolefin and cork materials.
When choosing a product from this very heterogeneous group, the installation should be done expertly by taking not only the substrate requirements but also the specific properties of the material into account. From a physical-technical point of view, the individual materials show a very different behavior. That’s in their nature. PVC coverings, for instance, are thermoplastic materials whereas rubber flooring consists of elastomeric materials. The term "thermoplastic" is derived from the two words "thermo" and "plastic". Materials are "plastic" when they change their shape (e.g. by the application of force) and afterwards retain their new surface morphology. Plasticine is such a material. "Thermo", the first part of the word, means that this change in shape can be induced by the influence of heat.
The most striking feature of elastomers, by contrast, is their elastic deformation. This phenomenon is known from rubber bands. The band can be forcibly stretched to a greater or lesser extent – in other words: deformed. As soon as the application of force stops, the band will bounce back to its original shape.
IMPORTANT!
In order to avoid costly complaints, it is absolutely essential to pay close attention to the substrate requirements and carefully consider the specific properties of the material.
IMPORTANT!
The correct installation of floor coverings depends above all on a detailed knowledge of the materials and their handling. For this reason, the installation instructions of the respective flooring manufacturer must be followed by all means!r
Thermoplastics (like PVC) are at one end of the spectrum while elastomers (like rubber) can be found at the other end. The properties of all other resilient floor coverings can be found somewhere between these two extremes. These physical differences alone make it necessary to adapt the installation to the respective type of flooring. Never make the mistake to underestimate the typical character of a floor covering.
Resilient flooring always calls for meticulously prepared, smooth and clean substrates. Any unevenness or soiling would inevitably show through the floor covering.
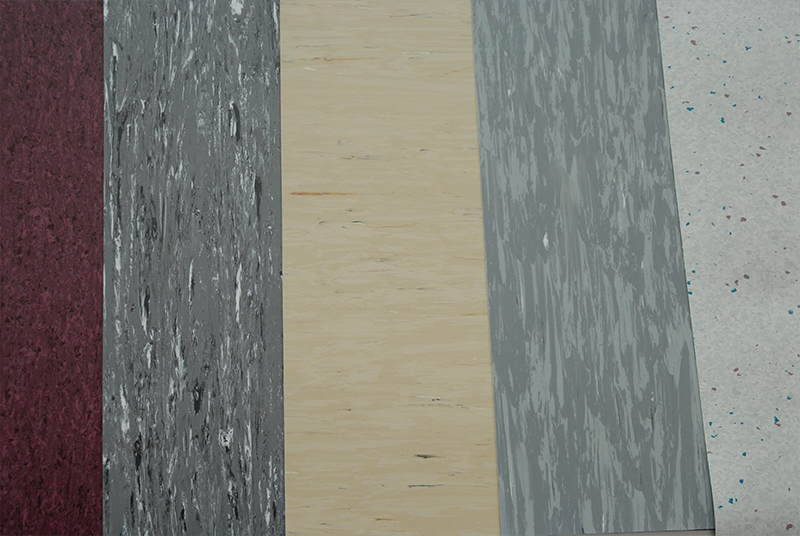
PVC flooring
The well-known acronym PVC stands for the thermoplastic material polyvinyl chloride. The stiffness of the plastic can be modified by adding plasticizers and stabilizers. PVC is easy to color, resistant to many acids, alkalis, alcohol and oil and absorbs hardly any moisture. These properties make PVC particularly well suited for use as a flooring material.
PVC flooring is very popular and finds widespread use in the form of sheets, tiles and planks. It is offered both as a homogeneous (single-layered) and heterogeneous variant (multi-layered, mostly with a decorative photo print). The heterogeneous variants are known under the term LVT (luxury vinyl tiles).
CV flooring
CV flooring falls under the category of PVC flooring. It is a two-layered material that consists of a textured PVC layer mounted on a foam backing. The letters CV stand for "cushioned vinyl". CV flooring is mainly available as sheet material.

Rubber flooring
Rubber flooring is extremely hard-wearing, impact sound damping, resistant to cigarette burns and able to withstand at least short-term exposure to diluted oils, fats, alkalis and acids. The bonding of this flooring material clearly differs from that of PVC.
An important factor of practical relevance is wettability. The wettability of rubber flooring continuously decreases over the flash-off time of the adhesive. While PVC flooring can also be installed by pressure-sensitive (or dry) bonding, rubber tiles and sheets require wet bonding. Contrary to PVC flooring, the wettability of the rubber floor backing ensures that a firm and reliable bond is established. As described in detail in TKB Technical Briefing Note 3 "Installation of Elastomer Flooring", rubber sheet flooring is usually bonded to absorbent substrates with a dispersion adhesive.
When subject to normal loads and low thermal stresses, rubber tiles are bonded to absorbent substrates with suitable Thomsit dispersion adhesives like Thomsit K 150, K 175 or UK 800. The product of choice on impervious, non-absorbent substrates is a reaction resin adhesive like Thomsit R 710 Polyurethane Adhesive. Alternatively, after consultation of a technical advisor, it is also possible to use the dry bonding system Thomsit DT 200 Quick-Lift Webbing. If high mechanical stresses are expected, e.g. pallet truck or forklift traffic, or when exposed to moisture, it is always recommendable to use a heavy-duty reaction resin adhesive like Thomsit R 710 Polyurethane Adhesive.
Linoleum
Linoleum, like all other floor coverings, can be bonded to sufficiently absorbent substrates using a dispersion adhesive. Even the typical bight marks (slightly wavy parts caused by the drying process in production when the linoleum sheets are hung in large loops between poles) can be reliably secured with modern linoleum adhesives. Due to a certain degree of water absorption and on account of the jute backing, a dimensional change already occurs when bonding the linoleum. In practical work, linoleum sheets are usually installed with a seam that corresponds to a postcard’s width (0.3-0.5 mm) to account for the fact that linoleum expands in width. Linoleum shrinks in length but expands in width. After applying a suitable adhesive with a trowel of notch size B1, the sheets must be pushed into the wet adhesive bed. Only a wet adhesive bed ensures the required wetting of the linoleum backing. If the open time of the adhesive is exceeded, this will result in insufficient wetting of the backing.
IMPORTANT!
The factory-cut edges of linoleum sheets may be uneven. Prior to bonding, they must be trimmed following the manufacturer's instructions. Before placing the curled edges into the adhesive, roll them back to flatten them out.
The following solvent-free Thomsit adhesives can be used for bonding linoleum:
- Thomsit K 175 Water-Based Contact Adhesive
- Thomsit L 240 D Dispersion Linoleum Adhesive
- Thomsit UK 800 Universal Flooring Adhesive
In special cases, e.g. on non-absorbent substrates, the linoleum sheets are bonded with Thomsit TKL 300 Fast-Fix Adhesive, a 2-component adhesive based on 1 part dispersion adhesive and 1 part cement powder.
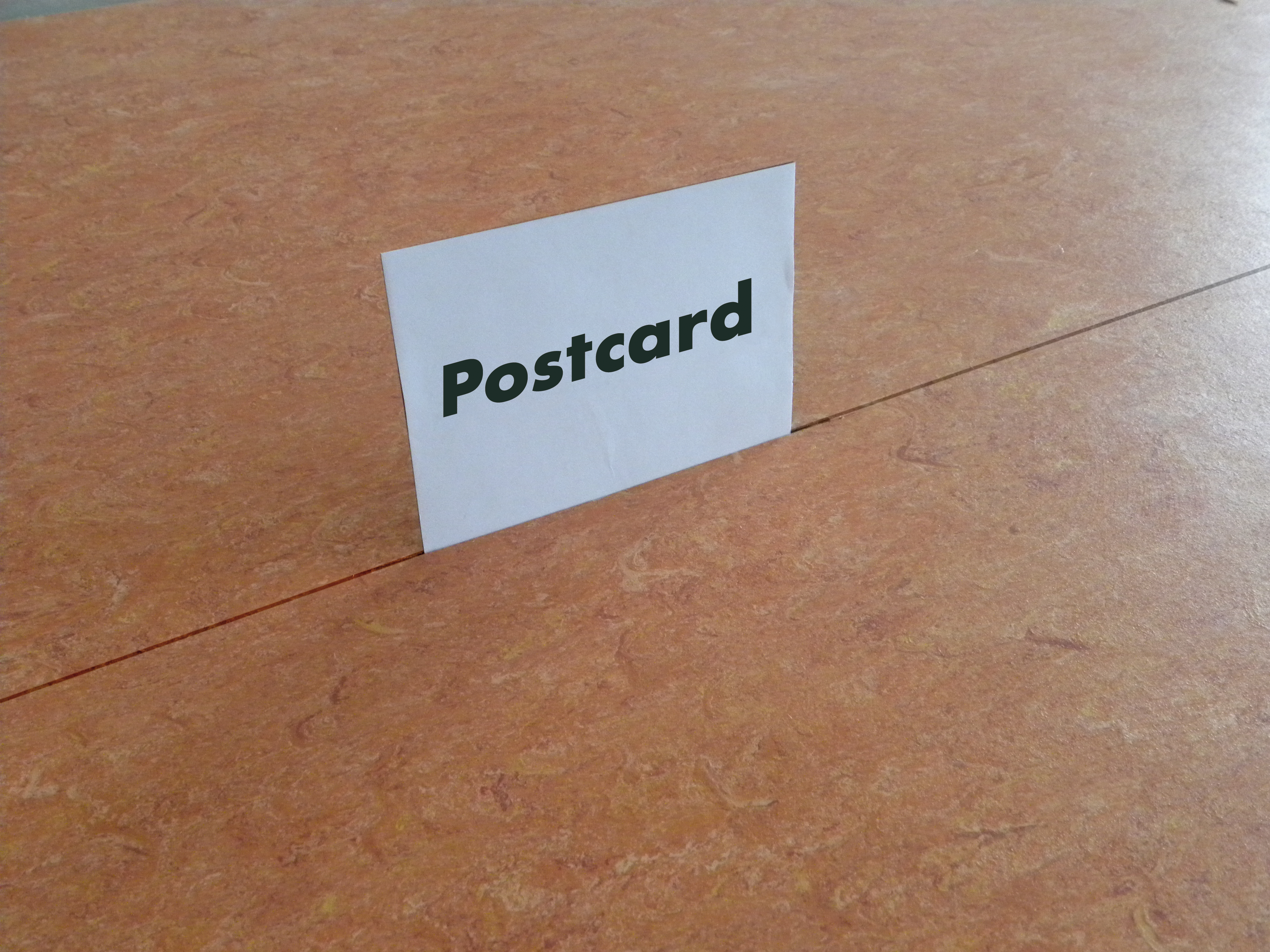
Wood flooring / parquet
Wood is a natural product and offers a number of advantages when used as a flooring material. The multitude of possible designs lends timeless beauty to any room. Naturally, wood tends to swell and shrink due to the moisture content of the wood. It is therefore liable to dimensional changes and makes high demands on the substrate. According to DIN 18356 "Parquet Works", it must always be ensured that the substrate is level, permanently dry, clean, free of cracks and separating agents and resistant to pressure and tension.
With due care, the parquet layer must therefore check whether the substrate is ready to receive floor coverings while observing the generally recognized rules of the trade, the state of the art, the regulations under VOB Part C (German construction contract procedures) as well as DIN 18356 "Parquet Works". The choice of a suitable adhesive depends primarily on the parquet type and wood species, the requirements to be met by the floor construction, the substrate to be covered and the specifications provided by the manufacturers of flooring installation products.
Make sure to follow the installation instructions given in the Technical Data Sheets.
The Technical Committee for Construction Adhesives (TKB) advises all floor layers to always check the technical necessity of using solvent-based parquet adhesives and to avoid them as far as possible since it is clearly the craftsman who bears the burden of risk. Until today, the instructions and requirements of TRGS 610 (Technical Rules for Hazardous Substances) have remained in full force and effect. For all difficult substrates, shear-elastic reaction resin adhesives offer the highest possible protection. As a rule, they are solvent-free and very low-emission, e.g. Thomsit P 685 or Thomsit P 695.
IMPORTANT!
The wood moisture of parquet always adjusts to the existing ambient conditions. Single-layer parquet made of solid wood must therefore be installed with a moisture content of 9 (± 2) %, multi-layer parquet with 8 (± 2) %. In addition, an air temperature of approx. 20 to 22 °C with a relative humidity of approx. 50 to 60 % must be observed.
In the interests of environmental and consumer protection, more solvent-free and very low-emission products should be used.
Thomsit P 618 Dispersion Wood Flooring Adhesive
Thomsit P 625 2-C PUR Wood Flooring Adhesive
Thomsit P 675 Elast
Thomsit P 685 Elast Universal
Thomsit P 695 Elast Universal Strong
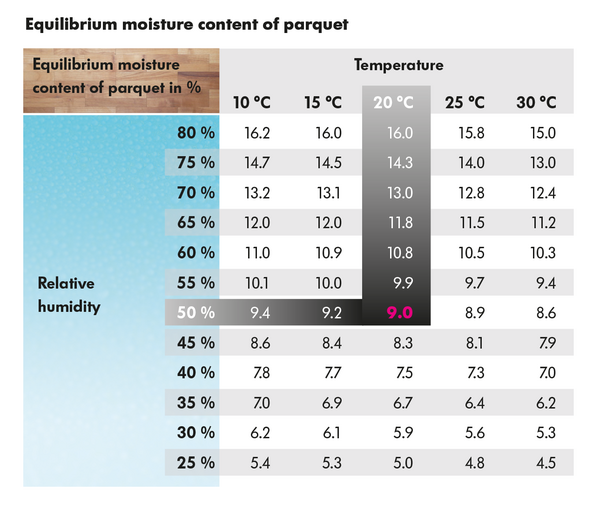